Latest Posts
How To Organise Your Commercial Storage Space
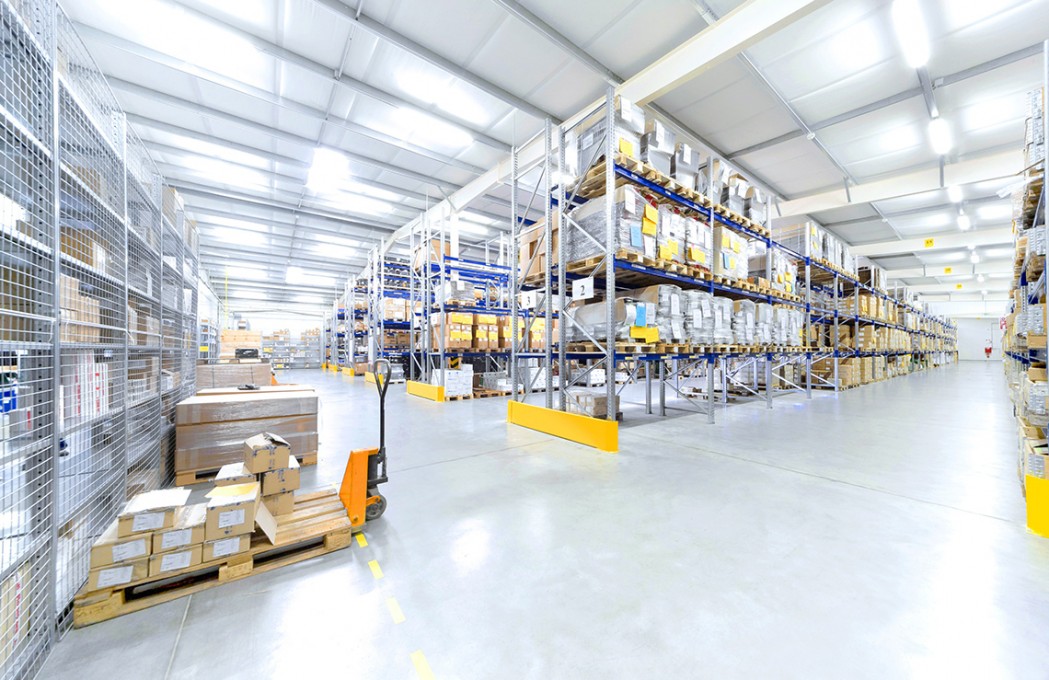
Inappropriately stored products, bottlenecks, inadequate shelving and poor team management can all contribute to a disorganised warehouse. Get your commercial storage space into top shape by assessing the best configuration for your business, and watch your product move out the door for years to come.
Take the time to analyse operations
Even if numbers are good and you’re operating in the black, taking the time to accurately assess how your warehouse is operating will do wonders to ensure the ongoing efficiency of your business. In an organised warehouse, you’ll able to spot bottlenecks without referring to inventory data. Take the time to reassess your picking methodology to ensure that it reflects your current sales patterns.
Label all products
This one should go without saying, but all products should be labelled. Depending on your inventory system, they should be ordered by unit number, with additional label details including type of product, description and barcode. Take this a step further and include digital pictures on your labels to save your team any guesswork when picking orders. Keeping boxes from being opened unnecessarily will save on both time and space.
Try stacking vertically
A warehouse that has run out of space is more than likely a disorganised warehouse without the right shelving solution. Save yourself from investing in unnecessary extra warehouse space by stacking vertically. After you’ve analysed operations, try to resolve bottlenecks and problem areas by creating extra space. Vertical storage can allow for a massive increase in product stored, however, appropriate safety precautions must be taken when determining the type of products to be stored on higher shelves, as well as the method of accessing them.
Find the rack system that works for you
Depending on the nature of your product - size, shape, or whether it is perishable or nonperishable, there are a number of rack and handling systems to choose from when organising your stock. Should you store products that require rotation to ensure freshness, a ‘first in, first out’ rack system will work best for you. Look for a ‘first in, first out’ rack that works efficiently and minimises manual labour. A push back rack system works best for products that won’t deteriorate with age, and that don’t rely on expiry dates.
Consider a redesign
Take what you’ve learned analysing your warehouse’s operations and consider a redesign in your shelving pattern. Keep aisle width in mind - ensure that your team and vehicles have enough room to move throughout the warehouse whilst optimising floorspace.
Safety first
Investing in the safety of your workers may not seem like an obvious step in improving the organisation of your warehouse, but it’s a more important investment than you may think. One of the biggest factors in warehouse inefficiency is accidents, and one of the top ten biggest causes of workplace accidents in the commercial storage industry relates to employee safety education - or a lack thereof.
Get your staff qualified in proper equipment safety in terms of driving forklifts, dealing with heavy loads and electricity, ventilation, and dealing with falling product. Ensure they’re always wearing the correct uniform, including gloves, shoes, helmets and protective eyewear. Make sure workers are correctly educated in avoiding stress and injury at work by teaching ergonomic stock handling practises.
Revise your safety plans and ensure that safety protocols are communicated across your team, particularly in regards to your pallet racking system. Make sure your shelving, tools and vehicles are kept up to date to prevent accidents and protect your staff and products. Keep your roofing and doors up to date and leak free. For a watertight roller door, install an ARD Commercial Roller Door.
Prioritise the placement of your most popular products
Go further than organising products by category, or ‘like with like’. Analyse sales patterns and gain efficiency by grouping together the 20% of products that make up 80% of your orders. This will reduce travel time for your team significantly. However, make sure that this area has the capacity to cope with high traffic, and maybe consider placing these products in a portion of your warehouse with wider aisles.
Use technology to speed up your processes
In this day and age, technologies that increase the efficiency of stock handling practises are developing rapidly. These innovations spam from the humble barcode to radio frequency, all the way to light and label technology, and even voice activated technology. Automated solutions, such as conveyor belts and multi-pick towers can provide extraordinary levels of productivity, efficiency and accuracy to your picking and packing process. Technology can at times be an expensive investment, but the returns on saved travel time and increased productivity can justify the cost.
Enjoy the benefits of an organised storage space
Taking the time to redesign and organise your warehouse is no easy feat, but it will pay itself off in no time. Watch your team locate product faster than ever before, in a safe and efficient environment.